Xnx Gas Detector Calibration 9
Xnx Gas Detector Calibration 9mm Price In India: Measuring gas appliances is essential to ensure that they are in good working order and can inform the user of gas hazards around them.
Measuring the “reset” detection of a detector is compared with the known filtering of detected gas in artificial air or nitrogen balance. This will determine the relationship between the detector’s study and the actual gas filter of the interest component.
Adjustments involve modifying the recipients’ responses to make the reading more consistent with expectations while introducing the tool to a known source. This is fundamentally different from briefly exposed electrical bump tests to ensure that sensors respond within a specific range and that detector alarms work correctly.
Why do we calibrate?
Calibration is needed for several reasons. If the instrument is placed under unfavorable conditions, this may lead to a change in the rate at which it responds to a given gas concentration. For example, the detector can read 46% LEL, where the actual rate is 50% LEL.
These conditions can include environmental factors, such as extreme temperatures or humidity, nerve toxicity through exposure to contaminants such as silicone and solvents, or exposure to high-concentration gases. Mechanical shock or stress and sensory age can also affect performance.
Besides, there is a need to demonstrate that regulations are followed as a record to show that particular metal is weighed and receives gas between the required tolerance is required. Instruments keep a log of their calibration date, which indicates when the calibration is performed and when it is expected to be subsequently, as well as produce a rating certificate as a record.
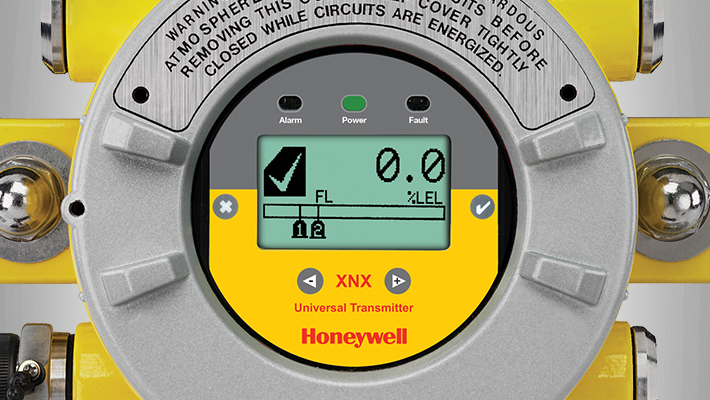
How do we calibrate?
When calibrating, it is essential to initially respond to flow patterns, flow rates, pressure, temperature, humidity, used gases, crossing sensitivity, sensory response time, and waste disposal, and follow any additional requirements indicated by the detector maker.
Power is usually a two-step process. First, the instrument is extracted from fresh air, artificial air, or nitrogen compound so that the reading is comparable to those expected in the fresh air. The second step is to expose the detector to the measuring gas containing a known concentration of sensor gases designed to measure and correct any deviations from the correct reading.
Alternatively, you can measure when using a particular type of gas and use the cross-sectional calibration feature to give you the answer to the required gases.
Read More:
How often should we calibrate?
The frequency at which an instrument is to be calibrated may vary. However, it is recommended that you combine data from the application with the environment and the user, manufacturer, and service provider. Risk assessments are often required to ensure that the calibration time is adequate. And remember, regular bump testing is recommended during calibration periods.
Multi-gas detectors and other detection technologies are essential in reducing workplace injuries and illnesses. Many dangerous atmospheric conditions cannot be detected by human senses alone, and equipment that can detect air in a closed space could mean the difference between life and death. However, equipment alone cannot protect lives unless employees are well trained in use and balance.
The gas appraisal is just another part of standard equipment testing, and it involves building a safe working environment. PK Safety experts have information and advice on proper detection calibration procedures to ensure that your gas reading is as accurate as possible.
Bump test
A bump test before using a gas controller is highly recommended and easy to perform. A bump test reveals gas monitoring sensors in the target gas to check if the alarm is moving before taking the controller to the field. The instruments should be zeroed before you test them to give the most accurate results.
Your monitor comes with a clip and a pipe for protection over the sensor plate; attach the other end of the pipe to the measuring and control voltage, open the controller and allow it, and then open the controller to allow enough gas to start the flow of the alarm on the monitor. This should take about 10 seconds but not more than 20 for the monitor to go off the alarm.
Comparing the monitoring study with the amount of gas present is the way you determine whether the controller is appropriately rated. If the response is within the acceptable tolerance range (the acquisition machine will provide acceptable tolerance levels), then the rating is guaranteed; if not, proceed with complete measurement.
Full Rating
If bump test results are not acceptable or after the detector has been used or severely damaged, the multi-gas detector needs to be fully measured. The complete measurement corrects the gas monitor readability and therefore responds to the gas test’s known pressure. Some disposable monitors come with instructions stating that no measurement is required for the metal’s life.
Still, for safety reasons, a regular check is vital to ensure that the device is responsive. The sensors in disposable monitors are the same ones used on unlimited life monitors, which are equally sensitive, and are subject to the same conditions.
Ensuring that your data is accurate is also essential for legal protection. The reading of many waves only holds in court as irrefutable if the gas detector is measured correctly before and after use to ensure its efficiency. Keep a written record of each tool’s life expectancy so that staff can identify what needs to be considered or are prone to inconsistent learning.
More Measurement Information
While you should follow the manufacturer’s guidelines for bump measurement and testing where possible, it is not always consistent between devices – except for those that use the same sensors. Many companies build their testing times for their monitors. Companies that use their devices daily typically measure every four to six months but bump testing is more common.
Our clients who use their monitors every 30 days or less usually rate each time the monitors go out to feel confident in their device responses. Check your equipment often if you suspect that conditions may affect their performance – such as toxicity, injury, or extreme weather conditions.
Pre-bump testing for each bulk gas can extend its measuring cycle for up to three to six months, according to data from RKI Instruments president in an article by the National Security Council. Standard assurance is acceptable in cases where the measurement is confirmed daily for 10 days in the target air, where no adjustment is required; no matter, the intervals between tests should never exceed 30 days.
OSHA requires businesses to measure gas testing equipment before each use. The International Safety Equipment Association (ISEA) recommends making sure the nerves respond to the gaseous precision test before use each day with a bump test. Device measurements should be made in areas where equipment will be used and in similar cases, if possible, to ensure that the reading is accurate in the actual field.